In the past production process
Tool life is usually measured in units of processing
 For example, a brand of tap claims:
Can process 10,000 pieces on 6061 aluminum alloy
M6*1 is an effective threaded hole with a depth of 15 mm.
But is the value here really useful to you?
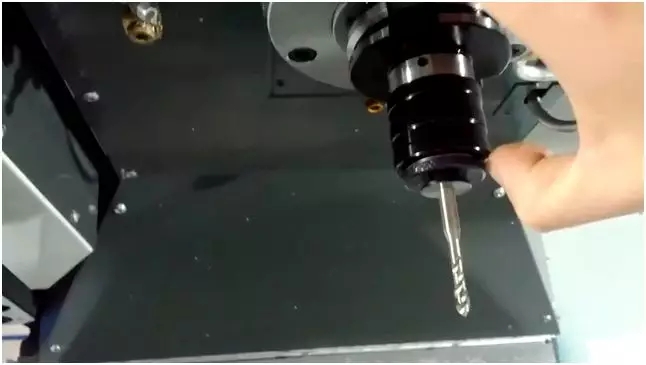
Tap at the time of testing
Usually on a single workpiece, even if 10,000 threaded holes are machined, the entire machining process (drilling the center hole, drilling the bottom hole, tapping) will not take a long time (usually less than 12 hours), and attack The quality of the bottom hole is carefully checked before the thread, and the quality of the cutting fluid is also guaranteed to be in good condition.
 Actual production
10,000 threads may be distributed over 1000 workpieces. It may take 40 minutes for a single process (including milling, drilling, reaming, boring, etc.) of the workpiece. It takes about 666.7 hours to process the 10,000 threaded holes. 27.7 days), during this time, the cutting fluid will be seriously degraded due to a large amount of impurities after cutting.
This seems to be very different from the situation at the time of testing. In the actual processing, there will be: the center drill wear, the drill bit wear, the drill bit breaks, the cutting fluid quality decline and many other factors that are not conducive to this thread processing. These uncertain factors will make the tap unable to reach the value at the time of testing.
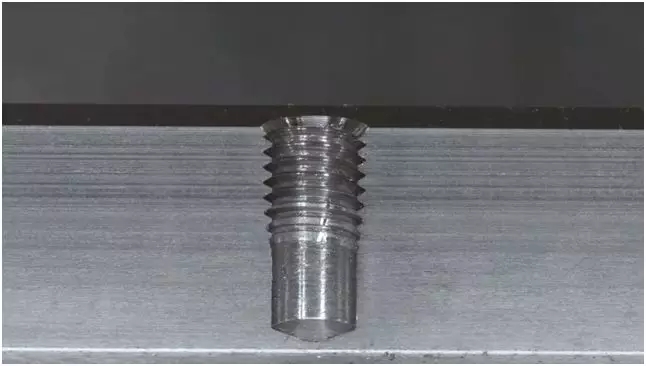
If these values ​​don’t mean much to me
What better way can I have?
 Here's a different way to consider:
The tap is broken because the torque value during processing is too large and exceeds the maximum torque that the tap can withstand, so that the fracture is caused. Therefore, monitoring the magnitude of the torque during machining means checking the state of the tool.
For example, a drill with a diameter of 5 mm can be processed well at 10Nm-20Nm through several consecutive measurements. When the temperature exceeds 22Nm, the quality of the machined hole is unqualified. The torque value of several bit breaks is 45Nm, 49Nm, 50Nm. 43Nm, 40Nm.
How does the machine automatically monitor these vital torques?
In the previous CNC system, the torque value was shown as the spindle load, and the torque range was expressed as a percentage (%). Only one maximum torque value was set. If it exceeded, an alarm will be issued: the spindle exceeds the load range!
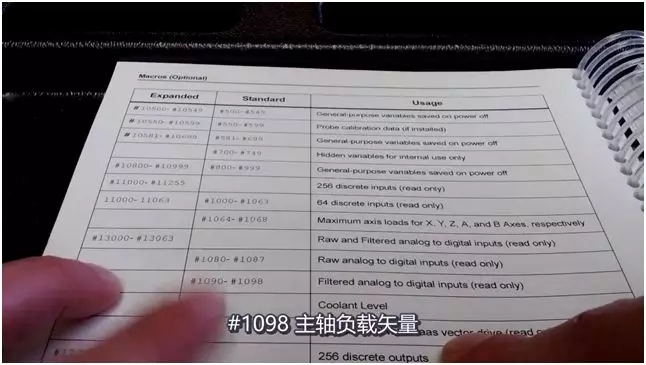
In Haas' latest CNC system (NGC), the load on the spindle can be displayed not only by the torque value, but also by the torque range of the tool in use in the tool magazine. For example, a drill with a diameter of 5 mm above:
Less than 1Nm (warning, indicating that the tool has been broken and suspending the program);
More than 1Nm and less than 20Nm (no prompt, the program runs as usual);
Less than 22Nm and greater than 20Nm (remind, inform the replacement of the tool as soon as possible to continue execution);
Greater than 22Nm (warning, indicating that the tool is in danger, any program that uses this tool will stop automatically when using this tool);
Note: The properties of each tool can be customized.
More than just drills and taps, all cutting tools can use this function!
This feature can greatly improve processing safety
For companies that process small quantities or single pieces
Significantly reduce production costs
I hope that you can use this function as soon as possible!
Â
Ungrouped
Isolation Board,Partition Panel,Opto Isolator Board,Isolation Foam Sheet Boards
SuZhou NiLin New Material Technology Co.,Ltd , https://www.sznlpc-sheets.com