Guilin Zhengdong Chemical Company White Latex Formulation and Process Flow Description: White latex is a kind of thermoplastic glue obtained by emulsion polymerization of vinyl acetate, polyvinyl alcohol, dibutyl phthalate, octanol and ammonium persulfate. . Widely used in the bonding of wood processing, wood-based panels, cement mortar, paper, cloth, leather, ceramics and other industries. It is easy to use, strong in bonding and simple in production process. However, its viscosity is unstable, especially in low temperature conditions in winter, and it often causes gelation due to increased viscosity. It needs to be heated before it can be used, which not only brings a lot of inconvenience to winter construction, but also affects the bonding quality. Therefore, the storage conditions are generally required to be above 10 °C. In response to this shortcoming, domestic and foreign scientific research workers actively develop low-temperature non-gelling white latex to solve the problem of winter storage and construction. The following preparation methods are introduced for their performance and use, for your reference.
System One:
1. Raw materials:
(1) Vinyl acetate: also known as vinyl acetate, abbreviated as vinyl acetate, colorless flammable liquid. Has a strong fragrance. Its vapor is irritating to the eyes. Do not dissolve in water, soluble in most organic solvents. Used in the manufacture of vinyl resins and synthetic fibers. Also used in the manufacture of rubber, paint, adhesives, etc. Used as a binder in this agent.
(2) Polyvinyl alcohol: a polymer compound obtained by saponification of polyvinyl acetate. White or creamy yellow powder. With thermoplasticity. Depending on the degree of saponification, the product is soluble in water or can only swell. It is mainly used as a raw material of a polyvinyl acetal resin, and is also used as a binder, a dispersant, and the like. Used as an adhesion aid in this agent. Use industrial products.
(3) Dibutyl phthalate: a colorless liquid. Do not dissolve in water, soluble in organic solvents such as ethanol and ether. It is a plasticizer for plastics, synthetic rubber, artificial leather, etc. It is also a solvent and curing agent for perfumes. Used as a plasticizer in this agent. Use industrial products.
(4) Octanol: Octanol has n-octanol and various isomers. This refers to 2-ethylhexanol-1. A colorless liquid with a special odor. Soluble in water and organic solvents such as ethanol and ether. This agent is used as a solvent. Use industrial products.
(5) Ammonium persulfate: a colorless monoclinic crystal. Sometimes it is slightly light green and soluble in water. It decomposes when heated and has strong oxidizing properties. Used as a bleaching agent, oxidizing agent, deodorizer, etc. This agent is used as a polymerization initiator. Use industrial products.
2. Formula (% by weight)
Vinyl acetate 45
Polyvinyl alcohol 5
Dibutyl phthalate 4
Octanol 1
Ammonium persulfate 0.1
Water 44.9
3. Preparation method (1) Dibutyl phthalate is mixed with octanol according to the amount of the formulation, and stirred to dissolve.
(2) Water was added to the vessel, heated to 70 ° C, polyvinyl alcohol was added under stirring, the temperature was raised to 90 ° C, and the temperature was maintained until all dissolved. After the dissolution, the heating was stopped to lower the temperature to 66 to 69 ° C, and vinyl acetate was added under stirring.
(3) The solution prepared in the step (1) is added to the solution prepared in the step (2), and finally ammonium persulfate is added, stirred and uniformly mixed, and emulsion polymerization is carried out at 66 to 69 ° C to obtain a white latex.
5. Method of use Depending on the object to be bonded, the stock solution can be used directly or diluted as appropriate. When diluting, first raise the emulsion to 30 ~ 40 ° C, then slowly add distilled water 30 ~ 40 ° C, not diluted with cold water. The amount of water added is preferably 20 to 30% of the stock solution. Too much water is added and the emulsification is destroyed, which can lead to failure. After dilution, add starch paste and other thickening.
When bonding wood, it is usually applied on two bonding surfaces, and should be left open for a while after coating. Usually, when the amount of glue is 100g per square meter, it is left for 5 minutes; when the amount of glue is 150g per square meter, it is left for 10 minutes; when the amount of glue is 200g per square meter, it is left for 20 minutes, then paste , and leave it for 20 minutes, and then press it for 3 hours or more with a pressure of 0. 294 to 0.490 MPa. It takes 8 to 16 hours to fully cure. It is also possible to adopt a heat curing method, which is generally pressed at a pressure of 0.294 to 0.490 MPa at 80 ° C after being dried until the adhesive is applied, and the thin plate only needs to be pressed for several minutes, and the pressing time of the thick plate is appropriately extended.
Method 2: Antifreeze white latex
(1) Raw materials "
1. Vinyl acetate (CH3COOCH=CH2) is abbreviated as vinyl acetate, a colorless flammable liquid with a strong aroma. Its vapor is irritating to the eyes with a relative density of 0.9312 (20 ° C). The boiling point of 72 ~ 73 ° C. Insoluble in water, soluble in most organic solvents, can be polymerized with other monomers. Here, it is a polymerized monomer of polyvinyl acetate, and an industrial product is used.
2. Polyvinyl formal is a resin obtained by condensing polyvinyl alcohol and formaldehyde. The raw materials are as follows: polyvinyl alcohol 100, formaldehyde 40, water 960 ~ 1040, hydrochloric acid (10%) 10.4 ~ 11.2, sodium hydroxide amount (adjust pH to 8 ~ 9), all of which are weight ratio. Used here as a modifier for white latex.
3. The emulsifier OP-10 [C8H17C6H4O(CH2O)10H]? The chemical name is octyl (or decyl) phenol polyoxyethylene (10) ether. The appearance is yellow or brown paste with a relative density of 1.06 and a freezing point of 7.2 °C. Dissolved in water, the aqueous solution is a transparent liquid, also soluble in carbon tetrachloride, lower alcohols and most aromatic solvents. Can withstand acid and alkali. Used here as an emulsifying dispersant. Use industrial products. Production plant: Guangzhou Auxiliary Chemical Plant.
4. Potassium persulfate (K2S2O8) White fine or large crystals with a relative density of 2.477, decomposed above 100 °C, and released oxygen to become potassium pyrosulfate. Soluble in water, insoluble in ethanol, strong oxidizing. Here, it is used as a polymerization initiator.
5. Sodium bicarbonate (NaHCO3) is also referred to as heavy sodium carbonate or sodium acid carbonate. Commonly known as baking soda, roasting soda or heavy alkali. White monoclinic crystal. The relative density is 2.20. In hot air, it can slowly lose some carbon dioxide and heat up to 270 °C to lose all carbon dioxide. It is an important common medicinal. This is used to adjust the pH. Use industrial products.
6. Dibutyl phthalate is a colorless, transparent oily liquid that is flammable and has an aromatic odor. The relative density is 1.045, the boiling point is 340 ° C, insoluble in water, soluble in organic solvents such as ethanol and ether. As a plasticizer here, the film formation temperature of the polymer can be remarkably lowered. Use industrial products. Production plants: Harbin Chemical Fourth Plant, Shanghai Solvent Plant, Tianjin Solvent Plant, Jinan Hongwei Chemical Plant, Guangdong Boshan Solvent Plant, Yunnan Xuanwei Solvent Plant, Hengyang Solvent Plant, etc.
(2) Preparation method 1. Formulation (parts by weight) vinyl acetate 16010% polyvinyl formal 180 emulsifier OP-10 2 water 30 potassium persulfate 0.4 sodium hydrogencarbonate 0.6 dibutyl phthalate 202. Operation The prepared polyvinyl formal is added to a reaction vessel equipped with a reflux condenser and a stirrer, and then an emulsifier OP-10 and water are added, and the stirrer is started to make it uniformly mixed. Then, 15% of the total amount of vinyl acetate and 40% of the total amount of initiator (potassium persulfate) were added. The temperature was raised by heating, and when the temperature rose to 66 ° C, reflux occurred. The temperature is controlled by the reflux rate. After the reflux is substantially disappeared, the temperature is raised to about 80 ° C, and vinyl acetate is continuously added at a rate of 10% per hour of the total amount of vinyl acetate, and the total amount of the initiator per hour is 4 ~. Add potassium persulfate solution at a rate of 5%. After the addition of vinyl acetate was completed in about 8 hours, the remaining initiator was added, and the temperature was raised to 90-95 ° C for half an hour. Finally, it was cooled to below 50 ° C, and a pre-mixed 10% aqueous sodium hydrogencarbonate solution and dibutyl phthalate were added, and the mixture was uniformly stirred.
(3) Appearance of product quality indicators Milky white, no particles and foreign matter pH value 4 to 5 viscosity (centipoise, 30 ° C) 5150 solid content (%) 46 to 50 ash (%) <0.15 film formation can be made without Color transparent continuous film bonding strength (Newton / cm 2) ≥ 2077 (normal) ≥ 759 (water resistant) gelling temperature is not higher than (°C) 2 (4) Usage and effect When using white latex, depending on the bonding target It can be diluted with water as appropriate. It is better to add 30~40 °C warm water when diluting. It is not advisable to use cold water. When bonding wood, the amount of glue applied can be determined according to the specific application, and the two adhesive faces are generally applied. After bonding, it is left for a while and then pressed for 3 hours with a pressure of 3 to 5 kg/cm 2 . At this time, the strength can reach about 70 to 80% of the bonding strength. It takes 8 to 16 hours to fully cure. If the method of heat curing is used, the curing time can be shortened, and it is usually heated and cured at a pressure of 3 to 5 kg/cm 2 at around 80 ° C. The sheet is only pressed for a few minutes, and the slab is extended for a suitable period of time.
Method 3: The production method of ordinary white latex:
1. White latex formula:
Raw material formula (parts by mass: %)
Vinyl acetate 46
Emulsifier OP-10 0.5
Polyvinyl alcohol powder 2.5
Potassium persulfate 0.09
Sodium bicarbonate 0.15
Dibutyl phthalate 5
Deionized water 45.76
Defoamer (tributyl phosphate)
(Note: The above white latex formula is for reference only)
2. White latex production process and process
(1) The polyvinyl alcohol powder was completely dissolved in deionized water and filtered. (Optional PVA-1788 2488, etc.)
(2) Put the polyvinyl alcohol glue into the stainless steel reaction vessel (the enamel reactor can also be used, but the heat transfer effect of the enamel kettle is not as good as that of the stainless steel reactor), then add the emulsifier OP-10, and start the mixer to mix it evenly.
(3) 15% (i.e., 6.9) of the total amount of polyvinyl acetate monomer and 40% (i.e., 0.036) of the potassium persulfate formulation amount were added to the stainless steel reaction vessel, stirring was continued, and the temperature was raised. When the temperature rises to 60-65 ° C, the heating is stopped. It should be noted that the initiator potassium persulfate should be firstly mixed with pure water to form an aqueous solution of 8% to 10%, which is added in multiple times.
(4) Under the action of the initiator, although the heating is stopped, the temperature rises by itself, and when the temperature is above 65 ° C, the reflux device of the reactor begins to reflux. When the temperature rises above 80 ° C, the reflux gradually decreases. At this time, the dropping of the polyvinyl acetate monomer was carried out from the dropping tank of the reaction vessel, and the dropping rate was controlled to be about 10% of the total amount per hour (that is, about 4.6). During the reaction, pay close attention to the reaction temperature, and add cooling water to the reactor jacket to control the reaction temperature, not higher than 80 °C.
(5) At the same time as the addition of the vinyl acetate monomer, the initiator is also added, and the amount per hour is about 4.5% of the formulation amount.
(6) Vinyl acetate and initiator should be controlled to be added around 8h. Due to the action of the initiator, the reaction is strong. After the monomer is added, the reaction temperature will rise by itself. When it rises to about 93 °C, it is kept for 30 minutes. The polymerization is almost complete.
(7) Turn on the cooling water to lower the temperature in the stainless steel reactor. When it drops below 50 °C, add sodium bicarbonate solution (10% concentration should be dissolved in advance) and dibutyl phthalate. The pH value is adjusted to 6~ 7 so far.
(8) The mixer of the stainless steel reaction kettle can not be stopped at all times. When it is cooled to room temperature, the finished white latex is obtained, and the stirring, discharging and packaging are stopped.
(9) When the viscosity of the white latex product is too large and the water resistance is poor, the amount of polyvinyl alcohol in the formulation can be appropriately reduced.
(10) If the stability of the white latex emulsion is poor, the amount of some initiators in the formulation may be appropriately reduced. When too little, the amount of the initiator may not be caused, resulting in difficulty in polymerization of the monomer.
(11) The amount of dibutyl phthalate should not be too much, not more than 10% of the monomer, otherwise the adhesiveness of the white latex finished product will decrease and the cost will increase. Its main role is to increase the toughness of the emulsion and reduce the film formation temperature of the emulsion.
(12) If the white latex finished product has more foam, an appropriate amount of defoaming agent may be added.
(13) The amount of initiator potassium persulfate and the addition time should be mastered. When the reflux starts, if the return flow is large, it indicates that the initiator has no effect. If the monomer is too much, the monomer should be stopped, and may be added as appropriate. Some initiators, when the reflux is normal, add monomer.
(14) The white latex produced by the above white latex formulation and production method is a white uniform emulsion liquid having a solid content of about 50% and a pH of about 5.
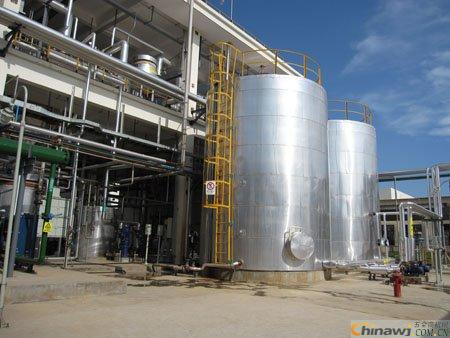
Solar Ground Screw we spread as one of the related solar energy product is very hot product on East-South countries and Europe countries. It is used by supporting solar panel brackets, Solar Mounting System, Solar Ground Mounting System and Ground Screw Mounting System. Building one solar energy plant on the ground, we recommend you to using solar ground screw as supporting , the U shape steel as the structures and solar panel as the main. Generally, we take the length 1600-2500mm and the diameter 76-114mm of solar Ground Screw Piles to ground solar mounting systems. According to your solar project detail plan, we will supply you the suited ground screw and if you don`t know how to choose, please contact us.
Solar Foundations
Ground Screw With Flange,Ground Screw Pile With Flange,Security Ground Screw,Security Ground Screw Anchor
Hebei Honde Industrial Trade Imp&Exp Co., Ltd. , http://www.groundscrewpile.com